Overview
AFE Crane, based in Cedar Falls, Iowa, installed a 5-ton capacity ACCO explosion-proof crane for lifting bulk container bags in a hazardous facility in Nebraska. As a distributor for ACCO Material Handling Solutions LLC, AFE Crane was tasked with replacing an existing motorized underhung single girder crane and extending the runway length from 60 feet to 120 feet. This confidential site required specialized equipment due to the presence of combustible dusts, which posed a significant fire and explosion risk.
Project Challenges
The facility’s hazardous environment required the new crane system to meet stringent safety standards for operation in a classified atmosphere. The existing crane, originally built in 1999, needed an overhaul to ensure compliance with modern safety regulations while accommodating the tight spatial constraints of the building. Additionally, the runway extension was necessary to provide access to new machinery in an expanded work area, demanding precision in the system’s design and installation.
The AFE Crane Solution
AFE Crane designed and installed a Class II, Group G, Division I explosion-proof crane with a 14-foot span and a 17-foot, 6-inch patented track bridge. The ACCO-Wright electric wire rope hoist operates at 30 feet per minute in single speed, with a lift height of 66 feet—the fastest speed achievable without compromising headroom. The single-speed trolley runs at 50 feet per minute, ensuring efficient material handling.
To meet the stringent requirements for classified environments, all hoist components, including the motor, motor brake, and conduit fittings, were labeled for Class II, Group G, Division I use. The Work-Rated hoist model was equipped with an overload device and a Weston-style mechanical load brake, providing an additional layer of safety. Radio remote controls further enhanced safety and efficiency, allowing operators to control the crane and hoist from a safe distance.
Project Execution
All crane components were carefully assembled and tested before installation to ensure compliance with operational and safety requirements. The installation team coordinated closely with the facility to integrate the new crane seamlessly within the existing space. The project included the installation of ACCO-Louden 585-style end trucks with eight 4.5-inch diameter wheels, steel wheel drives, and a 6-foot wheelbase. The system was completed with dual gimbal rod assemblies, a suspension system designed for under-running crane runways. This advanced suspension system allowed for structural flexibility, reducing the impact of building movement on crane operation.
Conclusion
The explosion-proof crane installation significantly improved the facility’s operational efficiency and safety by providing increased lifting capacity and extended reach while complying with strict hazardous environment regulations. The dual gimbal rod assemblies ensured smooth operation and optimal headroom, allowing the system to adapt to structural variations within the building. This project exemplified AFE Crane’s expertise in delivering specialized material handling solutions tailored to complex industrial environments. By integrating cutting-edge safety features and optimizing performance, AFE Crane provided the facility with a reliable and efficient lifting solution that meets the highest industry standards.
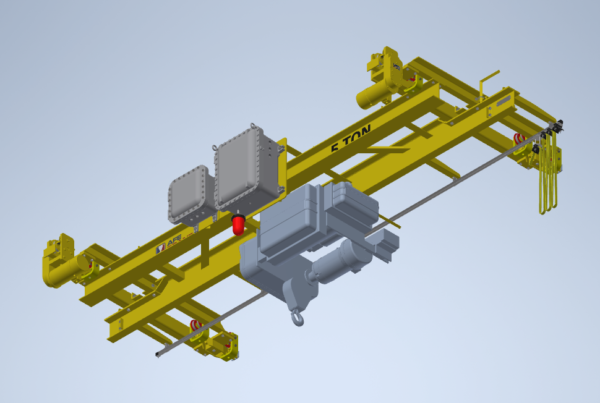
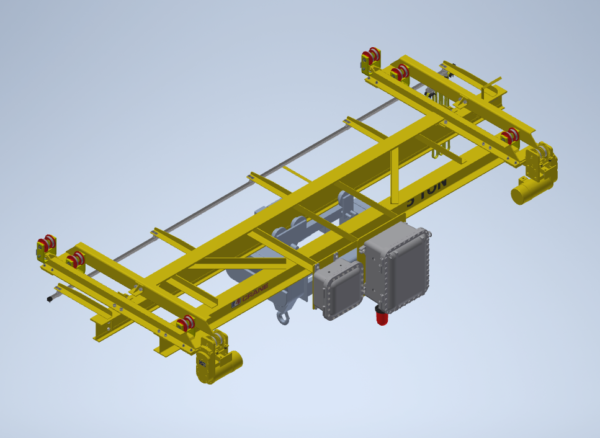