Overview
AFE Crane was selected to design and build a custom crane system for a manufacturer specializing in large outdoor commercial business signs. This company required a solution that could handle a diverse range of sign sizes, from small storefront displays to massive high-rise interstate signs. Precision, safety, and efficiency were critical in ensuring smooth lifting and transportation during the manufacturing process. AFE Crane developed a tailored system to meet these demands, providing enhanced flexibility and control.
Project Challenges
The primary challenge was designing a system capable of accommodating varying sign sizes while maintaining efficiency and ease of operation. The solution needed to support small, medium, and large signs without requiring constant adjustments or extensive manual intervention. Additionally, the control system needed to be user-friendly yet advanced enough to manage complex lifting operations seamlessly.
The AFE Crane Solution
To address these challenges, AFE Crane engineered and installed a dual 3-ton crane system on a 60-foot runway, with each crane featuring two 1.5-ton hoists. This configuration provided exceptional versatility, allowing the hoists to function independently for smaller signs, operate in tandem on a single bridge crane for medium-sized signs, or combine one hoist from each crane to manage large, elongated signs. This innovative setup ensured efficient handling of all sign sizes, minimizing downtime and maximizing productivity.
For precise and reliable control, AFE Crane integrated the advanced Magnetek Flex EX2 system, specifically the FLEX-12EX2-6RS-10M model. This system was chosen for its ability to streamline complex crane operations while maintaining user-friendly functionality. The setup included two bridge receivers and four carrier receivers, enabling seamless communication and control. Operators could independently control each bridge and carrier, optimizing workflow efficiency. The intuitive button configuration allowed easy bridge selection with buttons 1 and 2, while buttons A, B, C, and D managed the carriers. This type of transmitter provided robust and secure communication, ensuring reliable operation throughout the facility.
Project Execution
The installation of the crane system was coordinated and completed by a local general contractor. AFE Crane completed the final commissioning, starting up the cranes, function testing, and load testing. Rigorous testing and operator training ensured that the new system met all operational requirements while enhancing overall safety and efficiency.
Conclusion
The custom crane solution provided by AFE Crane significantly improved the manufacturer’s workflow, reducing handling times and enhancing production efficiency. The flexibility of the setup allowed for smooth transitions between different lifting tasks, aligning perfectly with the client’s need for adaptability. The manufacturer, known for its commitment to quality and creativity, expressed high satisfaction with the system’s performance and the ease of use offered by the Magnetek Flex EX2 control system.
This project highlights AFE Crane’s expertise in developing tailored lifting solutions that address unique manufacturing challenges. By leveraging cutting-edge control technologies and innovative engineering, AFE Crane continues to deliver solutions that enhance operational efficiency, safety, and client satisfaction. The manufacturer remains a leader in the commercial sign industry, benefiting from the enhanced efficiency and flexibility of their custom crane system.
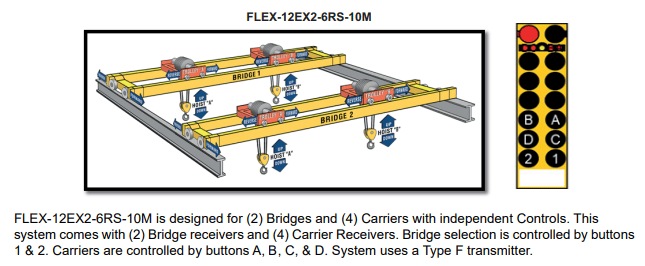