Overview
AFE Crane installed a custom hoist and crane system featuring over 1,000 feet of monorail track and 20 specialized hoists at the manufacturing facility of an outdoor lighting manufacturer. As a strategic distributor of ACCO Material Handling Solutions LLC AFE Crane was tasked with designing a system to move large light stands efficiently through the assembly process. The final installation included 20 custom wire rope, air-operated hoists equipped with double sister hooks, allowing light stand assemblies to rest securely as they progressed through production. Shuttle cranes were incorporated into the design to maximize efficiency while maintaining a compact footprint.
Project Challenges
The manufacturer, Musco Lighting of Muscatine, Iowa, needed to expand production capacity by doubling its existing production lines. The goal was to recreate and enhance an existing monorail system originally installed by AFE Crane in the 1990s, which had delivered consistent performance for decades. The new system had to integrate seamlessly into a 63,000-square-foot expansion while maintaining compatibility with the facility’s workflow. Coordination between AFE Crane, the manufacturer, the architect, and the building manufacturer was crucial to ensure the structure could support the monorail system. Additionally, the installation required careful planning to accommodate the diverse sizes and weights of light stand assemblies.
The AFE Crane Solution
AFE Crane designed and installed a system consisting of 1,240 feet of ACCO Louden monorail Supertrack, integrated with 11 switches and four custom shuttle crane stations. The monorail, standing 18 feet high, covered 24,000 square feet within the expansion area. The system enabled Musco to expand from two to four production lines, significantly increasing output. The hoists, featuring double sister hooks, accommodated light stand sections ranging from 3 feet by 5 feet to 22 feet by 10 feet, with weights between 50 and 500 pounds.
Shuttle cranes provided additional flexibility by allowing hoist trolleys to move perpendicular to the monorail, ensuring efficient transitions between workstations. The system was designed so that all hoist trolleys could be fully loaded and operate bumper-to-bumper, with extended bumpers protecting the loads from impact. Operators required only basic lifting safety training due to the system’s intuitive design.
Project Execution
Manufacturing and installation spanned four months, with all monorail components provided by ACCO, including curves, switches, hangers, and trolleys. AFE Crane oversaw the design, detailing, and construction of the shuttle cranes and hoists. The system structure was designed and built into the facility’s framework, requiring extensive collaboration among stakeholders. Despite last-minute modifications, the system fit seamlessly within the building, streamlining the installation process. A two-person crew completed the on-site installation in just a few weeks.
Each workstation featured an air hose pendant, allowing operators to connect to hoses descending from the hoist trolleys to control the hoists. When a trolley moved to the next station, the air pendant controls were disconnected. Safety baffles deployed automatically when the shuttle was in operation, preventing trolleys from running off the monorail.
Conclusion
The custom monorail system provided Musco Lighting with enhanced flexibility and efficiency, enabling smooth movement of diverse product sizes along the production line. The integrated switches allowed operators to remove trolleys from the main line for assembly while other products continued moving through production. The successful collaboration between AFE Crane and Musco resulted in a well-coordinated, highly functional system that met the manufacturer’s production goals. By leveraging decades of expertise and innovative engineering, AFE Crane delivered a robust material handling solution that optimized workflow and increased manufacturing capacity.
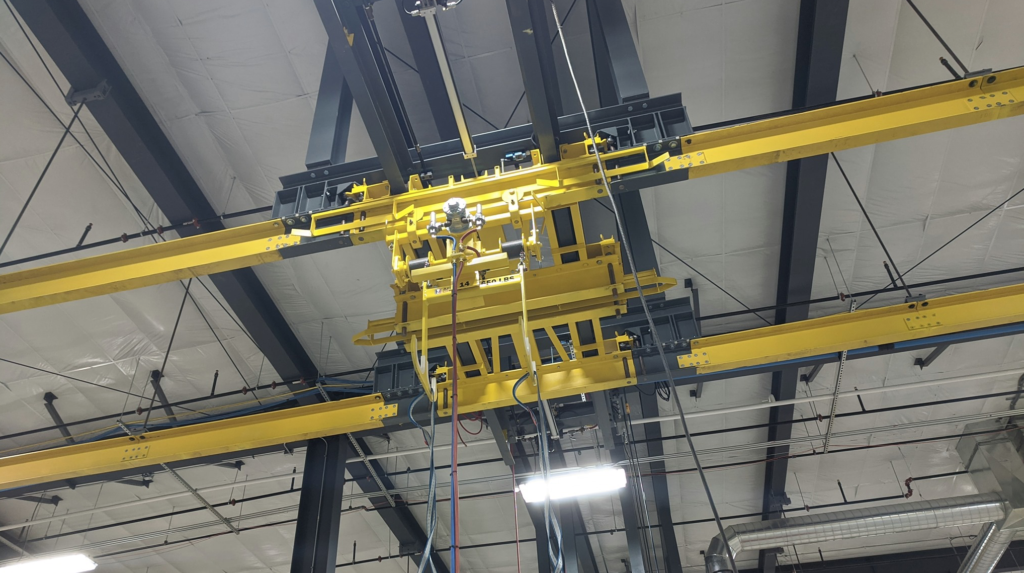
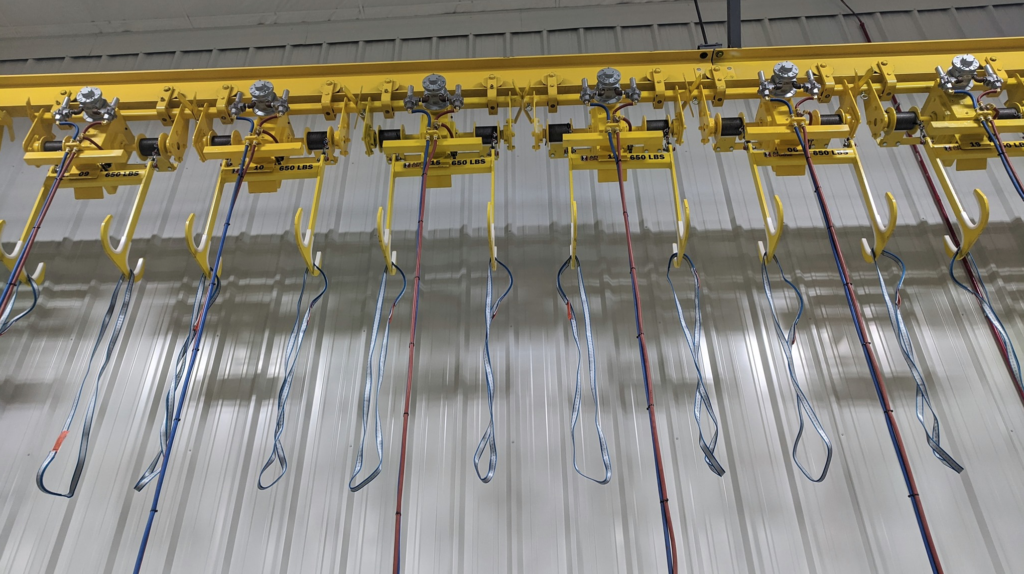